What are the common faults of electric vehicle controllers and how to repair them?
The controller of an electric vehicle is one of the four important parts of an electric vehicle. It is the "brain" of the electric vehicle. It controls the start, operation, advance and retreat, speed, and stop of the electric vehicle motor. If the controller has a problem, it will be difficult to move. So the "health" of the controller is very important! At ordinary times, riding should be cherished well, so that it can work better for you!
May 20,2024
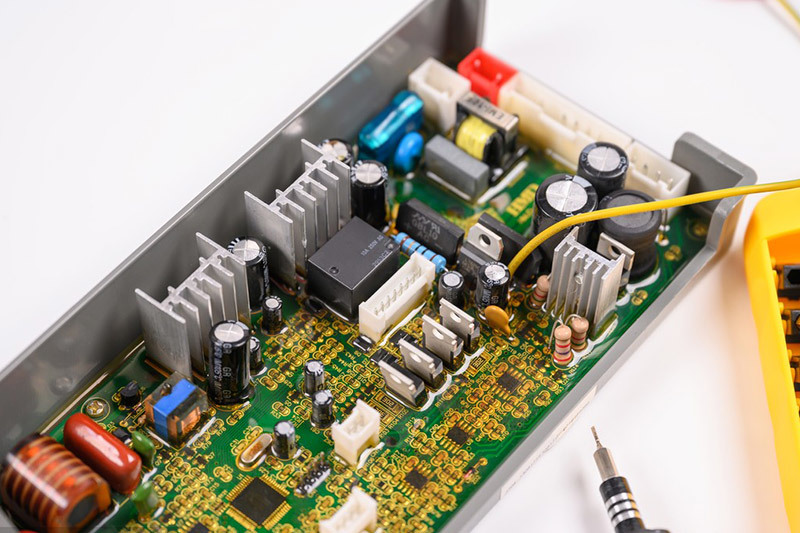
The controller of an electric vehicle is one of the four important parts of an electric vehicle. It is the "brain" of the electric vehicle. It controls the start, operation, advance and retreat, speed, and stop of the electric vehicle motor. If the controller has a problem, it will be difficult to move. So the "health" of the controller is very important! At ordinary times, riding should be cherished well, so that it can work better for you!
Problem 1: The electric car has a lot of noise when riding and slows down with load. After the car is stopped, the car cannot start at zero. Only when the motor rotates can it run normally.
Diagnosis and maintenance: This is a symptom of motor phase loss. Now the controller is mostly intelligent, and it will shake due to phase loss and zero start. This may be the motor Hall damage caused by the "sick state", there is a possibility that the controller internal a phase line circuit problems. After carefully checking whether there is a problem with the connecting line, if the Hall and connecting line are all tested normally, then the internal components of the controller have failed, please replace the controller!
Tips: When replacing the controller, be sure to fix it, tighten the anti-skid screws with "anti-skid" screws to avoid bad road conditions and bumps causing damage to the original controller by virtual welding and short circuit! At the same time, some functions should be connected as far as possible. Don't try to save trouble. If the functions are not connected, just turn the motor. The brake is cut off, the cruise speed is fixed, the three-speed shift and so on should also be connected! Avoid damage and trouble in the next three-pack period. With a little effort, after-sales worry!
Question 2: The electric vehicle will not be powered on and will be laborious for implementation. When it is implemented, it will make a "thumping" sound.
Diagnosis and maintenance: This situation is that the motor line is short-circuited due to contact with virtual connection. The three thick phase lines of the motor can be unplugged, and the phenomenon of pushing the cart disappears, indicating that the controller is broken. Please replace it. If it is still difficult to implement, the problem of the motor may be caused by short circuit and burn out of the motor coil.
Tips: If the power is turned on and the wheels do not turn, it is mostly an internal fault of the controller. Do not force the car to pull it when it does not turn. You can unplug any two of the three thick wires of the motor and it will be light! Otherwise, the forced drive will "pull" the motor and scrap it at the same time!
Question 3: The electric car can start normally, but it will not turn after running for a few meters.
Diagnosis and maintenance: The factors that cause this phenomenon are: 1. Insufficient power, and the controller plays an undervoltage protection state. 2. Check whether the circuit is in poor contact. When the speed rises, the current increases and the power is "blocked" and the power is cut off. This is often virtual welding! 3, the controller problem, the controller internal original welding or internal original damage. Electric vehicles have an undervoltage value. When driving to the undervoltage point, the controller will stop the power supply and ride or slow down. The 48V electric vehicle is 42V undervoltage point, and the 60V electric vehicle is 52V undervoltage point. 1. Turn on the power car lock, test whether the lock line voltage of the controller is available, test the 5V power supply line of the switch handle, the 5V power supply line of Hall, the high brake line of high level brake should be low level, and the high brake line should be high level. The low brake is opposite. The hand slowly toggles the motor wheel, the three phase lines of the controller have induced voltage, and the three signal lines of Hall (thin lines of yellow, green and blue) also change with rotation, there is a change voltage motor that Hall is normal! 2. Measure whether there is a signal in the handle. Please check the signal line of the handle. When the handle is not turned, the voltage is 0.8V-1.0V. When it is turned on, the voltage is 3.5V-4.0V. When it is turned on, the voltage is normal! 3: The brake is powered off, Hall, the handle is troubleshooting, or the power is not going, it is the controller fault!
Question four: the installation of the controller should pay attention to the main points.
The controller controls the motor. When connecting the controller, everyone must be careful and install it. The wiring should not be sloppy. The handle wire does not need a connector. Connect the handle wire directly and "wrap" it with insulating tape, because if the handle connector enters water, it will cause the car not to go or the speeding car will be out of control. There are also power lines and motor lines to be connected and welded with solder to avoid damage due to poor contact! At the same time, avoid burning the controller due to virtual connection or adhesion of the motor line!
Contact Us
E-mail :
Phone/WhatsApp:
+86-15967686999
Address:
Shangyun Village, Hengjie Town, Luqiao District, Taizhou City, Zhejiang Province